As a global leader in the auxiliary industry, Shini will show its principle of product development and innovation as well as its “one-station experience”by displaying the latest products, innovative technology and the most complete molding machine production line. Products and technologies Shini recommends for the Chinaplas 2014 are as follows:
Smart Modularization and Air Flow Control Technology
Modular products are practically widespread in modern industry. They can flexibly meet users’ actual demands with best economic and reasonable way according to their practical needs. Shini is going to display its development achievement of modular products in this exhibition. It’s a machine which is able to realize central dehumidifying and drying of multi materials via. convenient and fast assemble of standard parts.
Auto allocation technology of drying air capacity features that drying air of -40℃ is able to be allocated to each drying hopper automatically according to demands via. auto control system, which realizes reasonable use of drying air for reducing waste and avoiding over or lacking drying of materials.
Smart Modular Dryer SSMD consists of a rotary dehumidifier and three sets of modular drying hoppers. Those hoppers are set on the floor stand which is modularized assembly. The drying air comes out from the outlet of the rotary dehumidifier and goes out through the main pipe. Then, the drying air is sent to different drying hoppers via. the branches of the main pipe. After finishing drying, hot air will come out from the air exhaust outlet and then go back to the air return pipe. At last, it will go back to the rotary dehumidifier. During this process, this machine is capable of auto adjustment and allocation. There is an air flow transmitter and air regulator at each branch pipe which enters into drying hoppers. The air flow transmitter is for detecting air capacity changes and sends the related information to the central control unit which controls the air regulator to realize auto adjustment and allocation.
Refrigeration Technology with Industry Standard
For a long time, there is no correspond industry standard for water chillers. Most manufacturers use the refrigerating standard in air conditioner industry for designing water chillers. However, the working condition for water chillers used in industry is always largely different from the one for air conditioners. For example, the working ambient temperature for general air conditioners are 26~35℃ while water chillers require a more wide temperature range, like 10~30℃. For all reasons, water chillers produced according to standards of air conditioners is less reliable when applied in industry.
In order to improve the reliability of water chillers and to reduce failure rate of application, we amend the production standard as well as adopt total new internal structure and production technique, which makes them meet the actual demands in the industry environment better. Besides, we have a new type of dedicated controller for the water chiller of new type. The new controller can show the operation information in words directly, which is convenient for the users to watch the operation of the machine.
Integration Control Technology Basing on Ethernet
All new products introduced above have one same feature. They all can realize on-line connection with other industrial controllers. Integration control technology which is based on Ethernet is Shini’s innovative direction for future control system.
This technology can make all control devices which have communication functions connect by network through concentrator. The connecting way is similar to the one of computers. The main control unit realizes central control toward each other controller via. network. Meanwhile, each branch unit can be independently controlled. In other words, users can set the main control unit in the office or at other places for central control. Other branch control unit can be conveniently adjusted on the spot.
The demonstration system we display in this exhibition consists of the control panel of the molding machine and controllers of the auxiliary equipments. In this system, the control panel of the molding machine is the main control unit while the other five controllers of different auxiliary equipments are the branch control units. Therefore, the molding machine is able to centrally control different types of auxiliary equipments.
Auto and Fast Take Out of Large Plastic Products
At the show, Shini will display the new medium open double section type of three axes servo driven robot ST3-1200-1800MT which is based on the original large complete servo driven robot. All of its properties have been improved for fast operation. It’s suitable for two-plate mold and hot runner mold. It’s capable of all kinds of special actions, like arranging, stacking, quality checking and in mold placement, etc. It has obvious advantages in auto taking out refrigerator outer shell, air conditioner outer shell and automotive interiors. It also has features as follows:
•Position limit sensors and blocks at each axis can effectively prevent the operation from losing control;
•Possess 8-inch TFT high definition touch screen and user-friendly HMI;
•Have 3-point switch which comply with the safety standard in Europe and USA to minimize the risk of wrong operation;
•Come with a variety of languages for customers of different countries;
•Reserve auxiliary equipment interfaces to make it convenient for clients to add auxiliary equipments.
Smart Modularization and Air Flow Control Technology
Modular products are practically widespread in modern industry. They can flexibly meet users’ actual demands with best economic and reasonable way according to their practical needs. Shini is going to display its development achievement of modular products in this exhibition. It’s a machine which is able to realize central dehumidifying and drying of multi materials via. convenient and fast assemble of standard parts.
Auto allocation technology of drying air capacity features that drying air of -40℃ is able to be allocated to each drying hopper automatically according to demands via. auto control system, which realizes reasonable use of drying air for reducing waste and avoiding over or lacking drying of materials.
Smart Modular Dryer SSMD consists of a rotary dehumidifier and three sets of modular drying hoppers. Those hoppers are set on the floor stand which is modularized assembly. The drying air comes out from the outlet of the rotary dehumidifier and goes out through the main pipe. Then, the drying air is sent to different drying hoppers via. the branches of the main pipe. After finishing drying, hot air will come out from the air exhaust outlet and then go back to the air return pipe. At last, it will go back to the rotary dehumidifier. During this process, this machine is capable of auto adjustment and allocation. There is an air flow transmitter and air regulator at each branch pipe which enters into drying hoppers. The air flow transmitter is for detecting air capacity changes and sends the related information to the central control unit which controls the air regulator to realize auto adjustment and allocation.
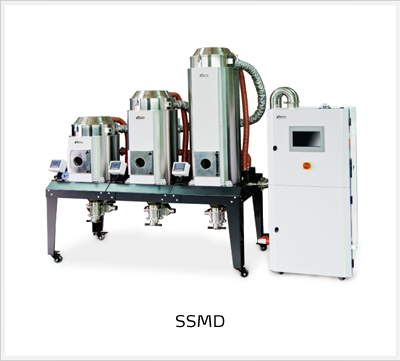
Refrigeration Technology with Industry Standard
For a long time, there is no correspond industry standard for water chillers. Most manufacturers use the refrigerating standard in air conditioner industry for designing water chillers. However, the working condition for water chillers used in industry is always largely different from the one for air conditioners. For example, the working ambient temperature for general air conditioners are 26~35℃ while water chillers require a more wide temperature range, like 10~30℃. For all reasons, water chillers produced according to standards of air conditioners is less reliable when applied in industry.
In order to improve the reliability of water chillers and to reduce failure rate of application, we amend the production standard as well as adopt total new internal structure and production technique, which makes them meet the actual demands in the industry environment better. Besides, we have a new type of dedicated controller for the water chiller of new type. The new controller can show the operation information in words directly, which is convenient for the users to watch the operation of the machine.
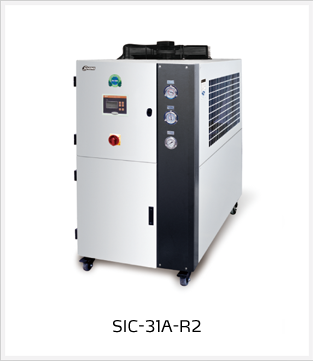
Integration Control Technology Basing on Ethernet
All new products introduced above have one same feature. They all can realize on-line connection with other industrial controllers. Integration control technology which is based on Ethernet is Shini’s innovative direction for future control system.
This technology can make all control devices which have communication functions connect by network through concentrator. The connecting way is similar to the one of computers. The main control unit realizes central control toward each other controller via. network. Meanwhile, each branch unit can be independently controlled. In other words, users can set the main control unit in the office or at other places for central control. Other branch control unit can be conveniently adjusted on the spot.
The demonstration system we display in this exhibition consists of the control panel of the molding machine and controllers of the auxiliary equipments. In this system, the control panel of the molding machine is the main control unit while the other five controllers of different auxiliary equipments are the branch control units. Therefore, the molding machine is able to centrally control different types of auxiliary equipments.

Auto and Fast Take Out of Large Plastic Products
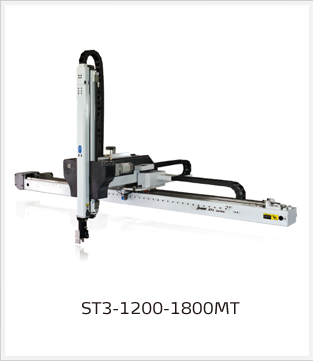
At the show, Shini will display the new medium open double section type of three axes servo driven robot ST3-1200-1800MT which is based on the original large complete servo driven robot. All of its properties have been improved for fast operation. It’s suitable for two-plate mold and hot runner mold. It’s capable of all kinds of special actions, like arranging, stacking, quality checking and in mold placement, etc. It has obvious advantages in auto taking out refrigerator outer shell, air conditioner outer shell and automotive interiors. It also has features as follows:
•Position limit sensors and blocks at each axis can effectively prevent the operation from losing control;
•Possess 8-inch TFT high definition touch screen and user-friendly HMI;
•Have 3-point switch which comply with the safety standard in Europe and USA to minimize the risk of wrong operation;
•Come with a variety of languages for customers of different countries;
•Reserve auxiliary equipment interfaces to make it convenient for clients to add auxiliary equipments.